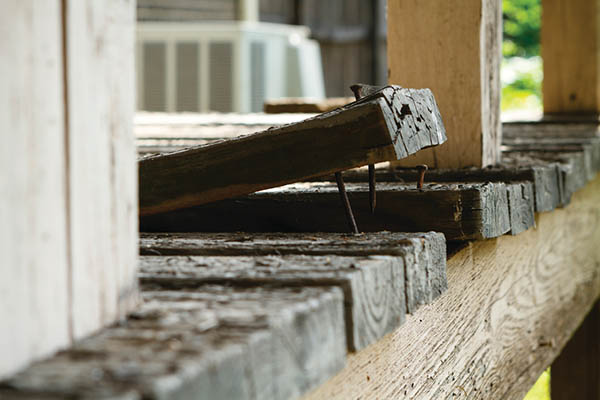
A wood deck is one of today’s most popular home improvements. With a new deck, homeowners create room for seating and cooking areas that make it easy to enjoy their outdoor spaces. Wood decking materials are sturdy and affordable, with a lifespan of fifteen years or more. However, exposure to the elements will take a toll on the wood from the beginning, so repairs may be needed just a few years after deck installation.
Wood deck materials are subject to several types of damage. Heat and UV rays from the sun cause drying, cracking and fading. Rain can soak into boards, causing them to expand and warp. Freezing and thawing throughout winter accelerates deck surface damage, and shifting ground can displace the posts. This damage is not only cosmetic; warped deck boards, loose stair treads and wobbly railings are dangerous. Accidental falls can cause serious injuries.
Inspecting Your Wood Deck
Because wood naturally absorbs water, it will absorb and retain moisture from rain, snow, irrigation, and even the soil around the foundation. While sunlit areas of the deck dry out quickly, shadier spots stay damp longer. Decks that are poorly ventilated or close to the ground also retain more moisture. These damp areas are the perfect spots for mold, mildew and fungus to take hold; left untreated, they eventually cause the wood to rot. Insects like termites also thrive in damp conditions.
Once the damage starts it can spread quickly, so it’s important to inspect your deck every year for weakness or damage such as:
- Wood rot
- Insect infestations
- Splintering or cupping deck boards
- Loose screws, bolts, and fasteners
- Weak or warped posts, joists, and beams
- Failed waterproofing
Types Of Wood Deck Damage
To decide whether an existing deck needs replacing, inspect all of its parts carefully to determine the extent of the damage. A basic deck inspection is an easy DIY that saves on labor costs by catching damage early. Make sure all metal hardware is in good condition and there are no bolts, screws or fasteners missing. Look carefully for water and insect damage, cracks and warping.
Pressure treated lumber is often used because it’s insect resistant – but it’s not insect proof! Insect damage and moisture issues are the main causes of a damaged deck, and replacing deck components regularly will greatly expand the lifespan of a wood deck. Inspecting the substructure underneath an old deck is also very important for safety reasons. This illustration shows all of the building components of a deck:
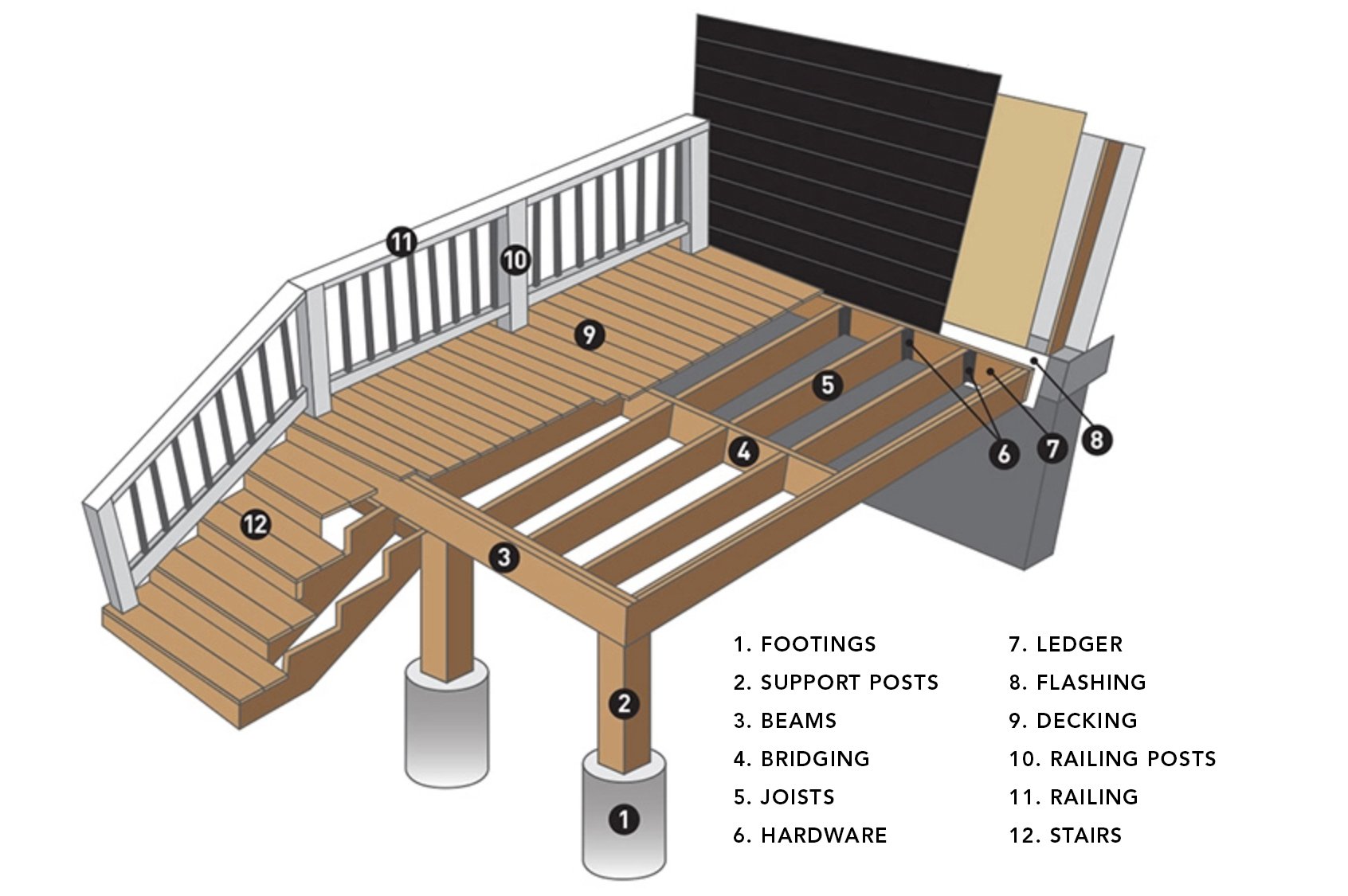
Deck Posts
Start your inspection with the deck posts. The posts support the entire weight of your deck, so it’s important to fix or replace any weakened or damaged posts. Most wooden decks are supported by 4” X 4” or 6” X 6” posts that are anchored to concrete footings. On many decks the posts are set into concrete below ground level. Newer construction methods anchor the posts with a metal bracket on top of a concrete footing or pier. The metal brackets provide a break between the concrete and the wood post for better protection from insects and moisture.
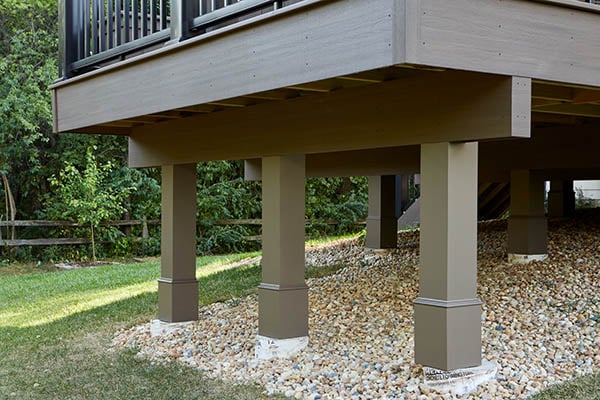
All posts should be carefully inspected for insect and moisture damage. Both water and termites travel through concrete, creating hidden damage that can compromise the structure. Make sure each post is firmly anchored at the footing and at the top where it joins the deck. Most wood-boring insects enter the post from the ground and moisture seeps up from the soil, so inspect the post bases thoroughly. Look for signs of warping, twisting or cracking. Poke a screwdriver firmly into each side of the post near the ground. If the screwdriver makes a hole or the wood is soft and spongy, you have insect or moisture damage. Small areas of damage can be repaired but if the damage is significant, the post should be replaced.
If several posts are damaged it’s probably time to consider deck replacement with a low-maintenance product like Timbertech AZEK or PRO Composite Decking.
Deck Beams and Floor Joists
Deck beams are large horizontal beams that rest on top of the support posts; a beam that is attached directly to the house is called a ledger beam. Deck beams form a frame that supports the floor joists, which are beams placed 12″-16″ apart within the frame to support the decking boards that make up the deck surface.
Deck beams should be securely attached to the house and to the posts with large bolts. While building codes vary in different locations, most deck beams are 2″x 8″ or 2″x 10″. Ledger beams should have a row of bolts on both top and bottom edges, set 2″ in from the edge of the board. Check for any missing or rusted bolts, and any sign that the deck is pulling away from the house.
Moisture damage is a common problem along the ledger board, because moisture can be trapped between the board and the wall of the house. Even pressure treated wood will eventually rot if it is constantly wet. Look for metal flashing along the top of the beam to keep the rain out; if there is no flashing, inspect the area carefully for moisture damage by poking along the beam with a screwdriver. Have a deck repair contractor install flashing to avoid future repair costs for damage to the ledger beam and the home’s siding.
Deck Boards
Deck boards cover the floor surface of the deck. On wood decks they are often made from pressure-treated pine; however, durable wood species like redwood and cedar have been popular in the past. Wood deck boards will eventually warp, split, or rot from exposure to the weather, especially in cold, wet climates. Check the entire deck surface for boards that are spongy, cracked, or feel loose. Use a screwdriver and pry bar to poke and pry them to make sure they are solid and firmly attached. Look for warping or cupping (when a board installed upside down curls upwards). All board edges should be flat and form an even, uniform surface.
Because wood deck boards are easily damaged by the weather, a popular upgrade is to replace them with new composite deck boards like Timbertech AZEK or Timbertech PRO.
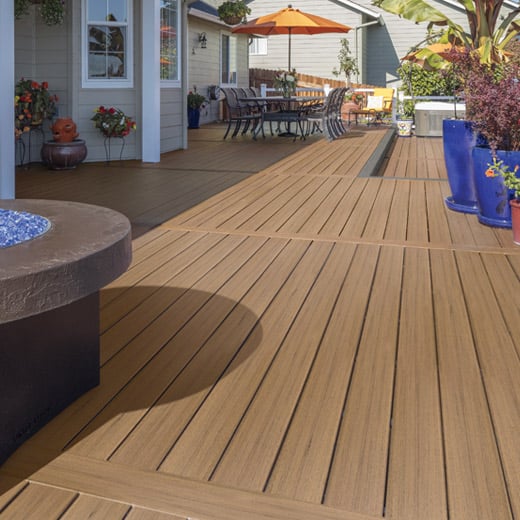
Deck Stairs
Whether your deck has just a few steps or a long flight, wood deck stairs take a beating from the weather and foot traffic. The stringers that support the stairs come in contact with the ground where they easily absorb moisture. Closed deck stair designs can trap leaves, snow and ice on the steps, making them more susceptible to rot. The stairs are also one area where deck building crews make mistakes, so check them carefully.
When inspecting deck stairs, be sure to check the connection between the stringers and the deck frame; they should rest against the face of the beam and be firmly attached with metal stringer hangers. The base of the stringer should be set on concrete, with a landing area of at least three feet across. Use a builder’s level to make sure that each step is level; angled stairs are a safety hazard and prevent water from draining properly. Look for missing deck screws, rotted or weak areas on the stringers, and stair treads that are splintering, spongy or cupping. Make sure the stairs have adequate lighting too; riser lights are an easy addition that puts the light right where it’s needed.
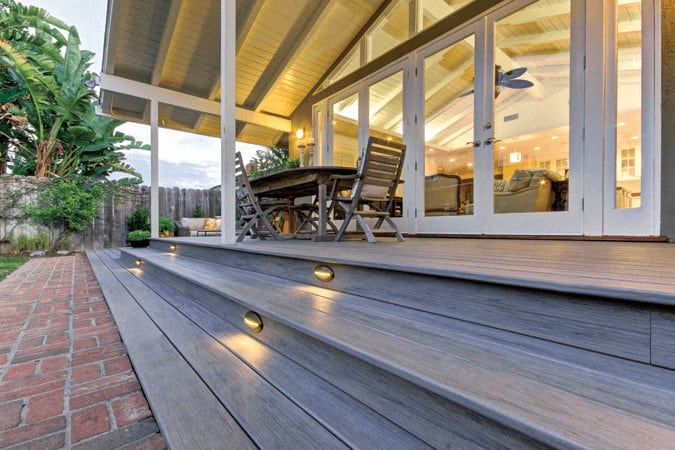
Deck Railings
Most building codes require a deck to have railings when it’s a certain height above the ground; a wood deck typically has wood or metal railings. For safety reasons it’s important to inspect the railings often and make sure they are secure. Each railing post must be firmly attached using long screws or bolts directly into the deck’s frame; it’s not safe to screw them to the surface deck boards. The balusters should be no more than 4″ apart and attached to the rails securely.
Check all railing sections for cracks, splintering and rotten or damaged wood, especially where the posts are attached. Make sure the railing does not move when you push firmly against it. Look for rough spots and splinters on the top rail and sand or scrape them smooth. To reduce future maintenance, replace wood deck railings with aluminum, PVC or composite. Post lights add an upscale touch while improving safety.
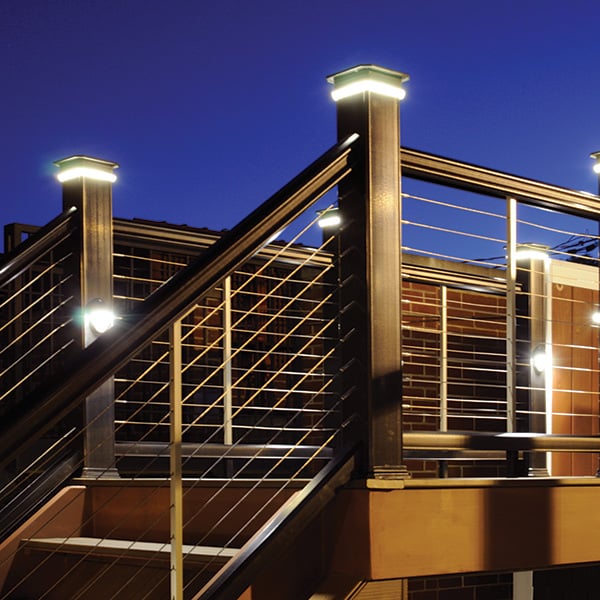
Weather Protection
The best way to extend the lifespan of a wood deck is to protect it from the elements. All wood deck materials should be sealed with either a clear deck sealant or a deck stain to help prevent water absorption and sun damage. Ideally, your wood deck should be cleaned every year and resealed every three years; more often if you live in a harsh climate. Test the sealant on your wood deck by dripping water on it; if the water creates beads then the sealant is working; if the water soaks in, it’s time to reseal the deck. Pay extra attention to stair treads, handrails, and any areas that have been sanded or repaired.
Is It Time To Replace Your Wood Deck?
Old, rotten wood decks are the cause of many accidents, so safety is an important issue. Replacing rotten or damaged components ensures a deck will remain safe and have a longer lifespan. It’s probably best to replace your wood deck if you find any of these 12 safety concerns:
- Undersized posts, beams or joists
- Cracked or warped support structure
- Height over 8 feet without extra bracing
- Missing or inadequate concrete footing
- Lack of metal joist hangers and bracing
- Undersized or too few bolts on beams
- Ledger beam not securely attached to the house
- Joists more than 16″ apart
- Sloping stairs with non-level treads
- Stair stringers attached incorrectly to frame
- Railing posts not bolted to the deck frame
- Balusters more than 4″ apart
It may also be smart to upgrade the deck to a more durable material if there are too many boards that need to be replaced. Often the wood substructure of a deck can be repaired and re-used for a brand new, low maintenance deck surface. Composite deck boards and railings of composite or aluminum are waterproof and insect-resistant, with a lifespan of 25-50 years.
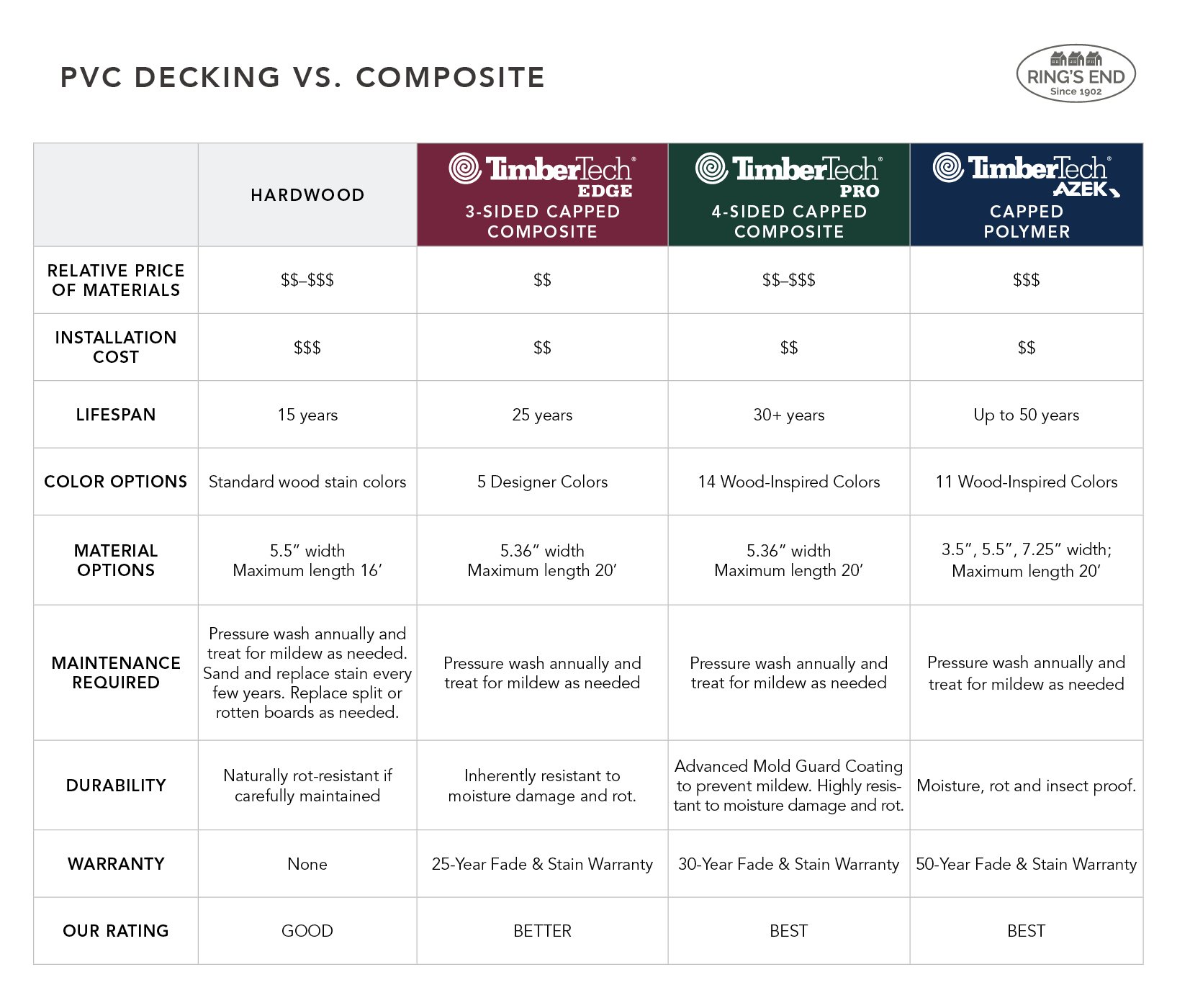
Where To Buy Deck Replacement Materials
Here at Ring’s End, we offer a wide selection of building materials in-store and online. We’re proud to offer TimberTech composite products, because we know that homeowners have confidence in their 30-50 year product warranty. Visit a Ring’s End store near you to get started today!